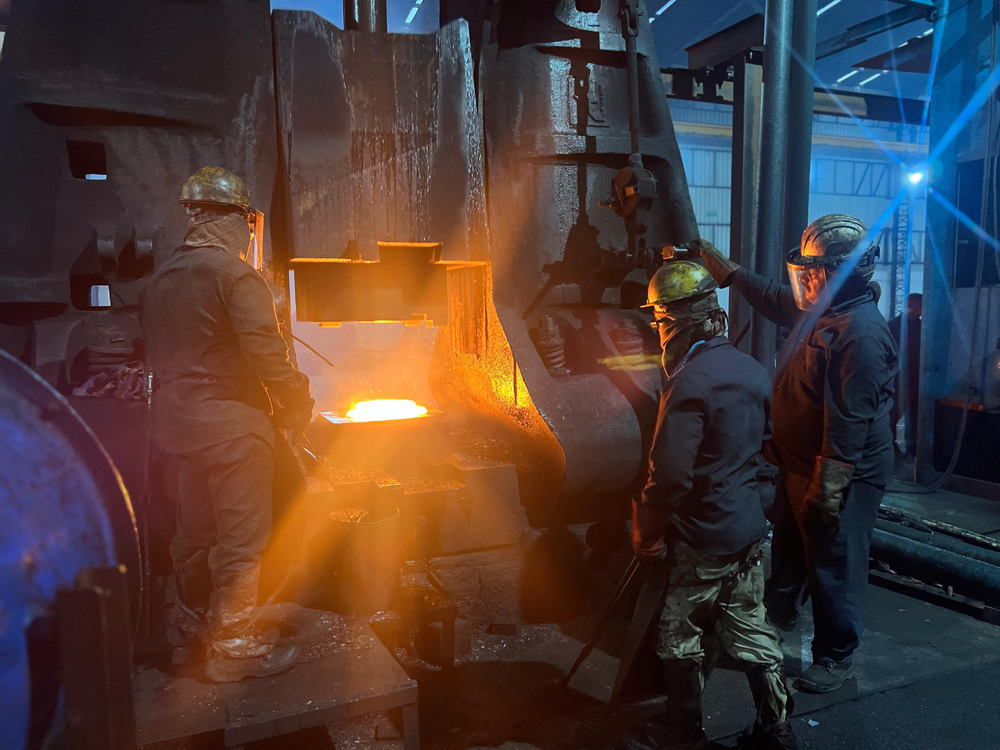
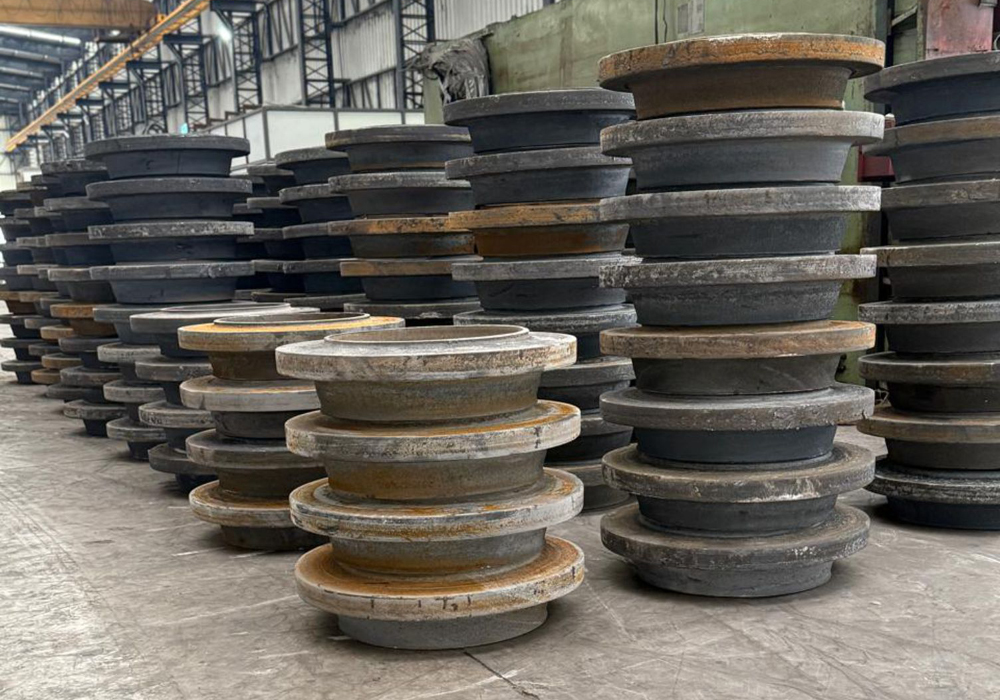
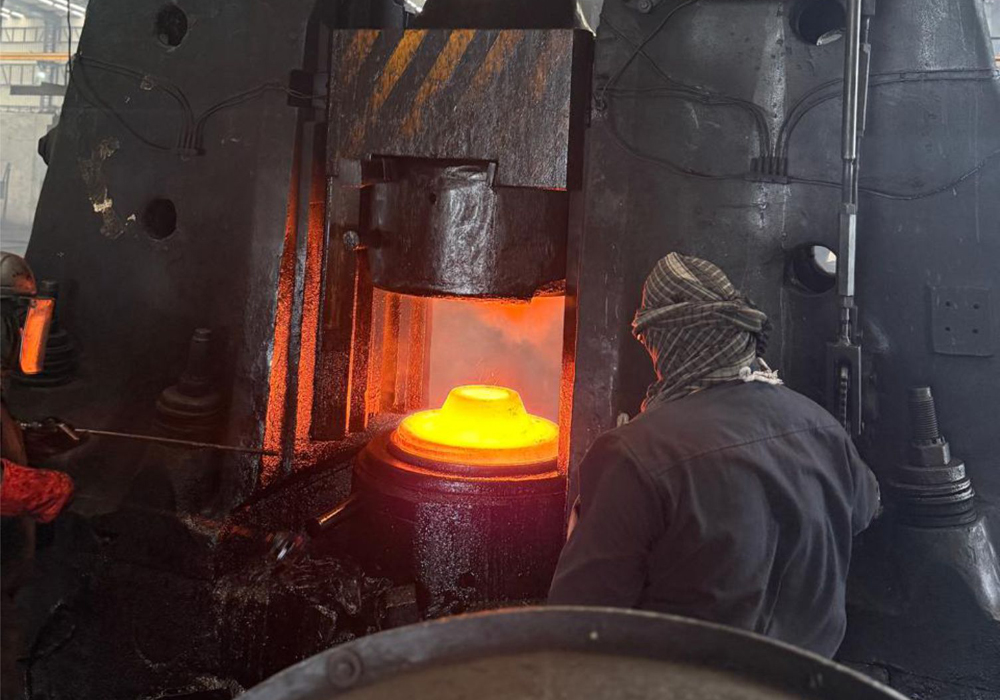
Up Setting Forging – Precision Closed Die Forging for Complex Components
At Shailesh Forging Works, our closed die forging facility is designed to produce precision-engineered, high-strength metal parts using advanced forging presses and tightly controlled processes. This method is ideal for complex geometries, delivering consistent, repeatable results with minimal post-processing.
Whether you’re in need of automotive, aerospace, oil & gas, or industrial machinery components, our closed die forging capabilities ensure near-net-shaped products with outstanding mechanical integrity.
What is Closed Die Forging?
Closed die forging, also known as impression-die forging, involves shaping heated metal by pressing it into a mold or die cavity that contains the inverse shape of the final component.
Advantages include:
- High-dimensional accuracy
- Excellent surface finish
- Superior grain structure and strength
- Little to no machining required
- Ideal for the mass production of parts with consistent quality
Closed Die Forging Capabilities
Our facility is optimized to deliver a wide range of forged components with precise control over weight, shape, and metallurgy:
- Weight Range: 20 kg to 350 kg
- Applications: Flanges, gears, levers, yokes, shafts, couplings, hubs, bearing races, and various automotive and industrial parts
- Materials Forged: Carbon steels, alloy steels, stainless steels, and specialty grades
Forging Equipment & Facilities
We are equipped with a fleet of heavy-duty hammers and presses that provide the force and control needed for repeatable, high-performance forgings:
- 4 Ton Zygmunt Hutta – 1 Unit (10000B)
- 6 Ton Zygmunt Hutta – 1 Unit (16000B)
- 8 Ton Russian Arrie – 1 Unit
These high-impact machines ensure:
- Excellent mold fill
- Superior part definition
- Uniform grain flow
- Low internal stress
Quality Control & Process Monitoring
Each closed die forging is subjected to a stringent quality assurance protocol, including:
- Dimensional verification
- Surface inspection
- Non-destructive testing (NDT) such as UT or MPI
- Heat treatment traceability
- Material traceability and certification
Our production and inspection teams ensure each component meets international standards and customer drawings.
Why Choose Our Closed Die Forging?
State-of-the-art forging technology
Superior tooling design for long die life
Competitive lead times
Enhanced mechanical strength and grain refinement
Cost-efficient for medium to high volume production
Reduced machining and material waste
Industries Served
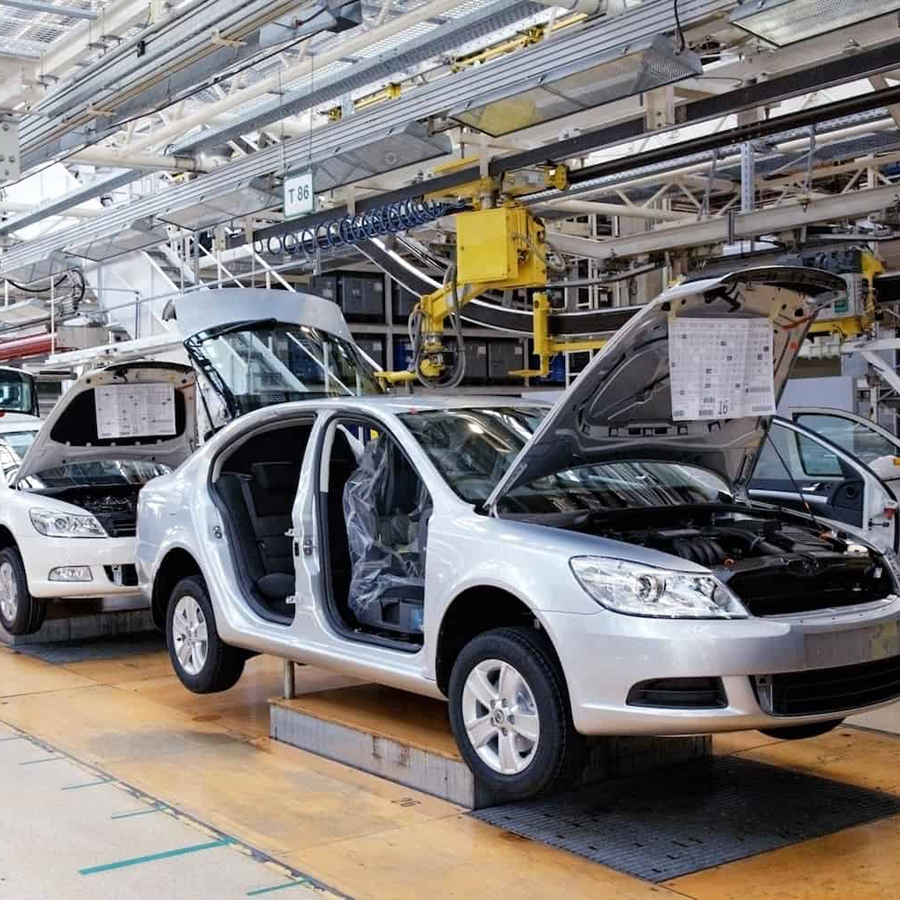
Automotive
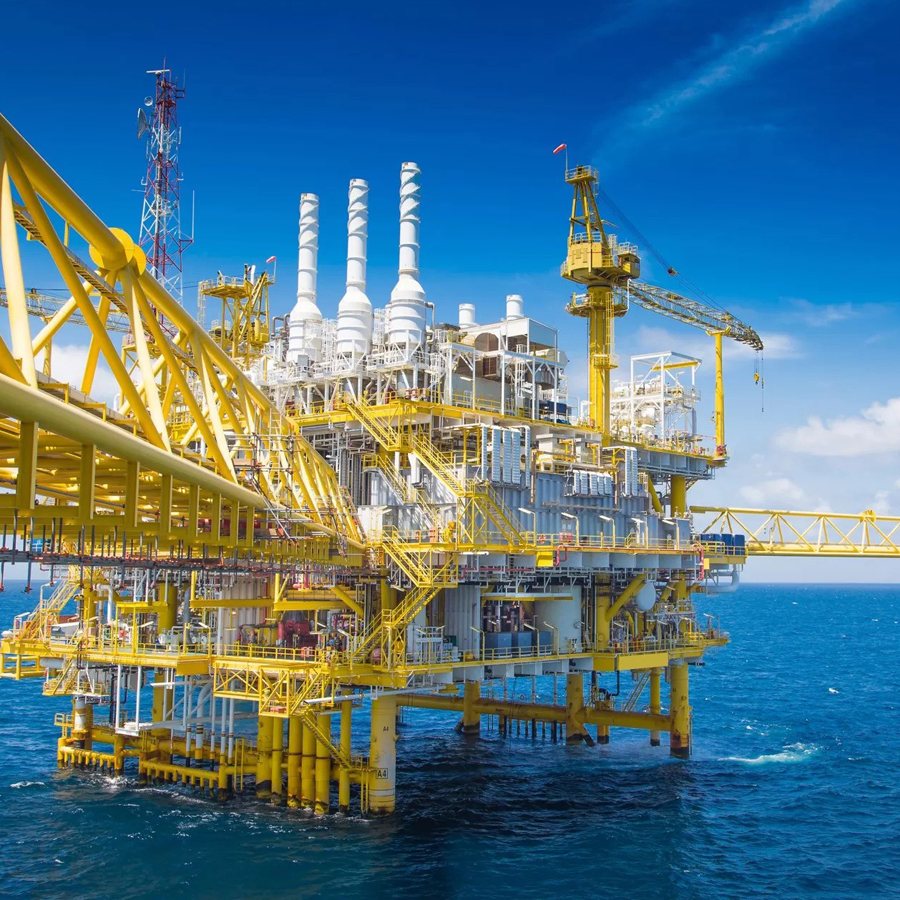
Oil & Gas
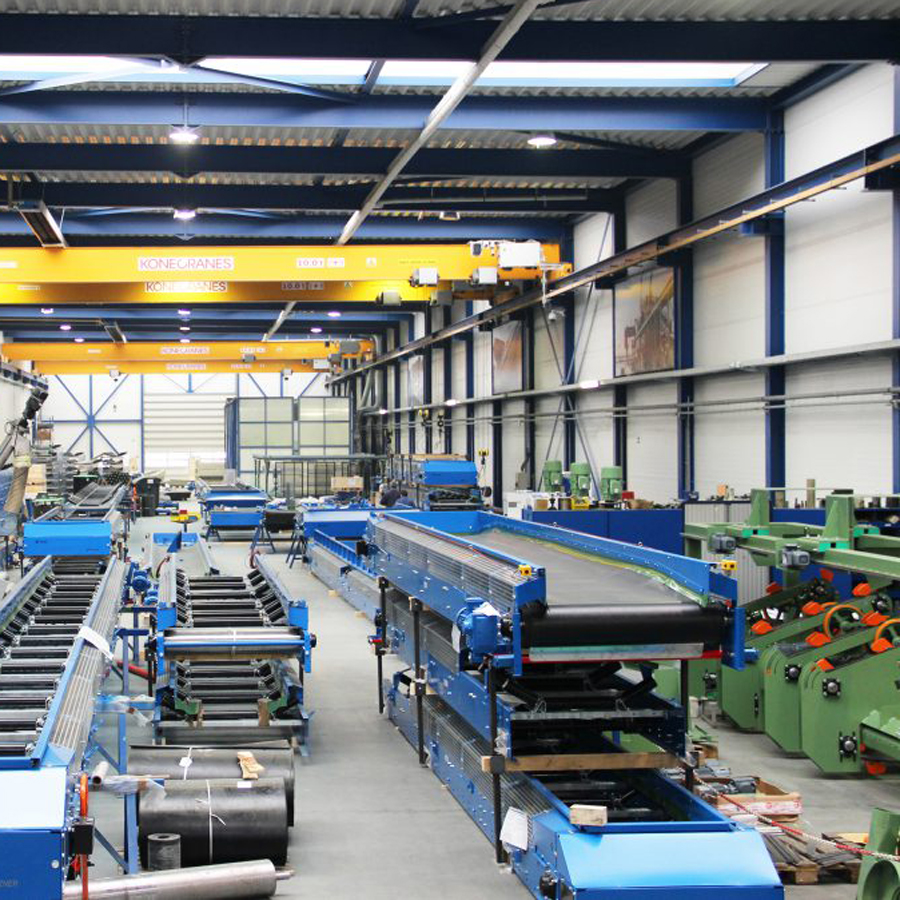
Industrial Machinery
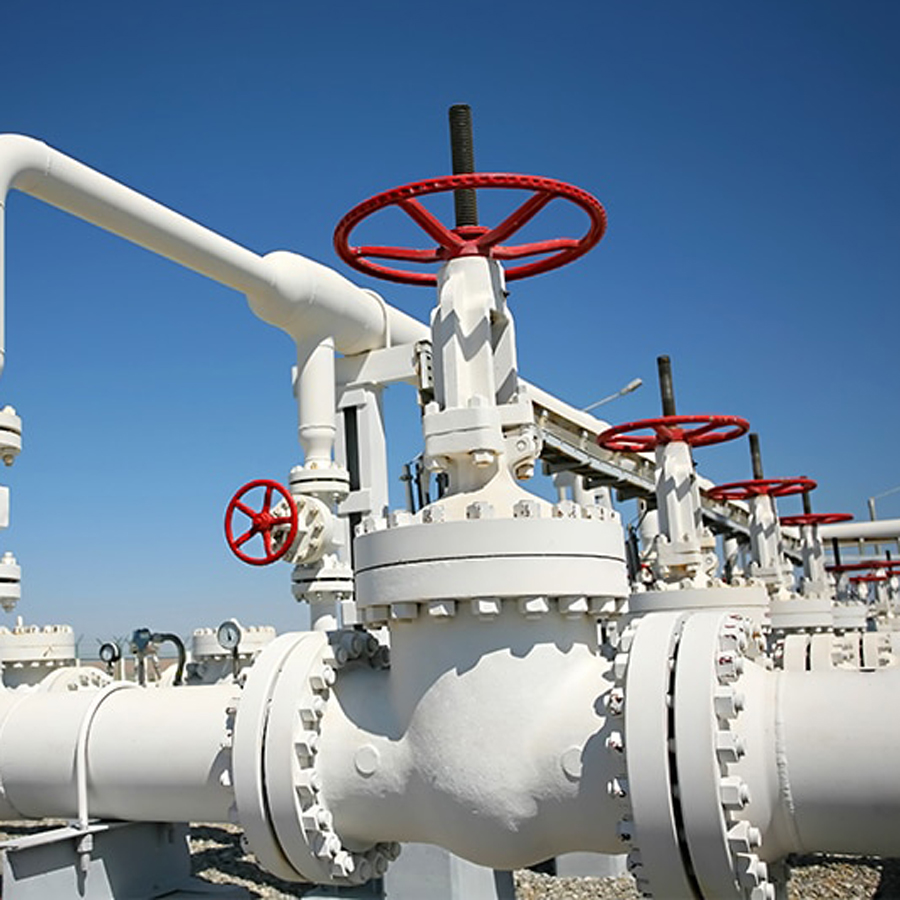
Valves & Fittings
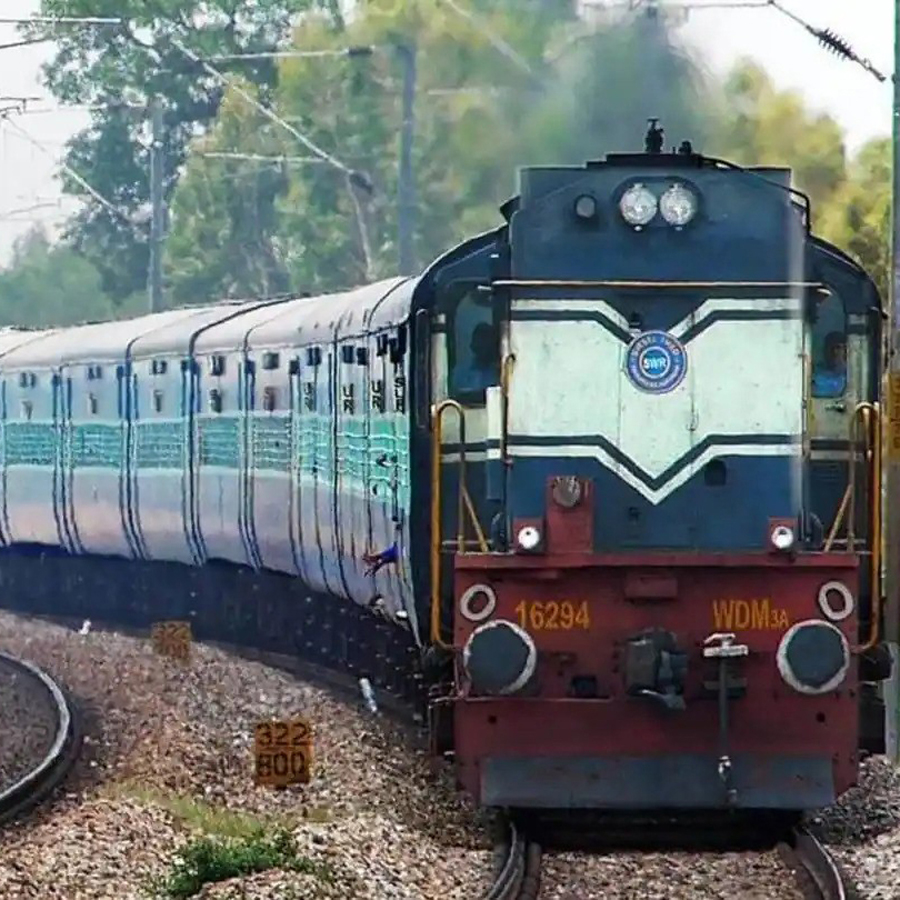
Railways
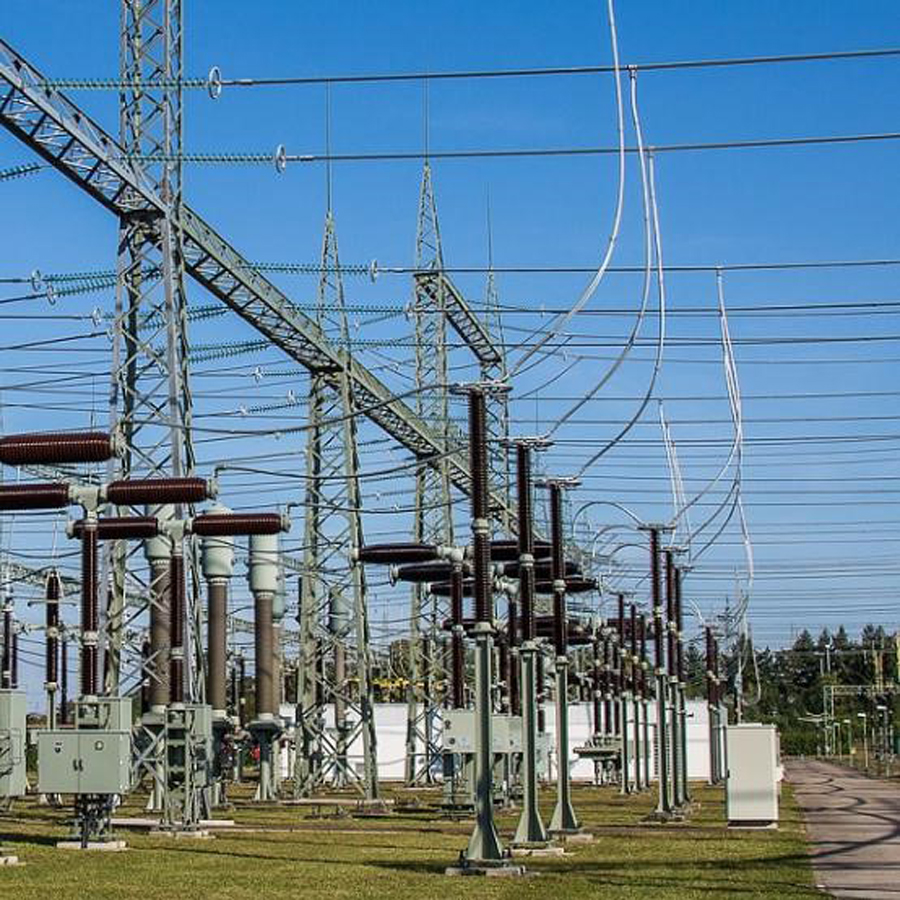