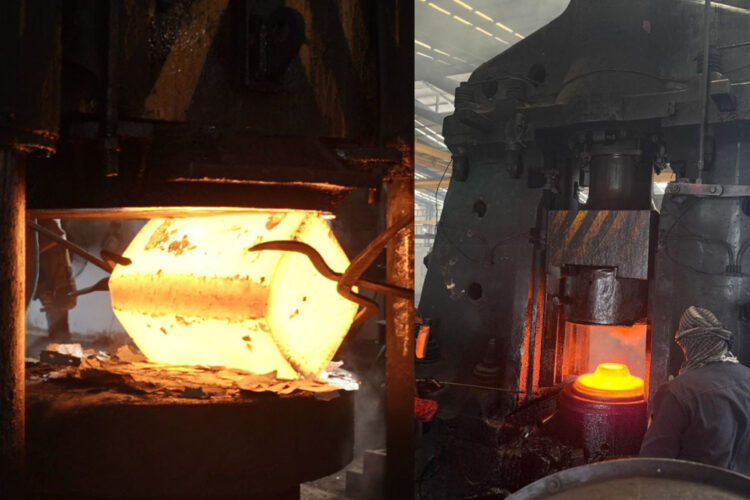
In the world of industrial metal forming, forging stands out as one of the oldest and most reliable methods to create strong, durable components. At Shailesh Forging Works, we specialize in both Open Die Forging and Closed Die Forging, catering to a wide range of applications across oil & gas, aerospace, power, and heavy engineering industries. But how do you know which forging process is best for your project? Let’s break down the differences between open die and closed die forging, and help you determine which one is ideal based on your part size, material, precision needs, and production volume.
What Is Open Die Forging?
Open die forging, also known as free forging, involves deforming heated metal between flat or contoured dies that do not enclose the material entirely. The metal is struck repeatedly until the desired shape is achieved.
Ideal For:
- Large parts such as shafts, step shafts, discs, and blocks
- Low to medium production volumes
- Custom and non-standard shapes
Advantages
- Excellent grain flow and structural integrity
- Allows for flexibility in size and shape
- Minimal tooling costs
- Best for large, heavy-duty components
Industries That Use Open Die Forging:
- Oil & Gas (e.g., shafts, rings)
- Aerospace & Defense (e.g., billets, bars)
- Heavy Machinery (e.g., gear blanks, hubs)
What Is Closed Die Forging?
Closed die forging, also called impression die forging, uses shaped dies that form the metal into a precise and repeatable net or near-net shape. The metal is placed into the cavity of the die and deformed under high pressure.
Ideal For:
- High-volume production
- Complex shapes with tight tolerances
- Components that require little to no machining
Advantages:
- High-dimensional accuracy and repeatability
- Great for the mass production of smaller parts
- Enhanced surface finish and detail
- Reduces waste and machining time
Common Applications:
- Automotive components (e.g., gear blanks, levers)
- Valve parts and flanges
- Power transmission components
Feature | Open Die Forging | Closed Die Forging |
Tooling Cost | Low | Moderate to High |
Part Size | Large | Small to Medium |
Tolerances | Less precise | Very precise |
Design Flexibility | High | Limited |
Volume Suitability | Low to Medium | Medium to High |
Lead Time | Shorter for one-offs | Longer (tooling setup required) |
How Shailesh Forging Works Delivers Both
At Shailesh Forging Works, we are equipped with:
- Open Die Forging Capacity: Up to 4 MT, with 2500 MT Hydraulic Presses and Drop Belt Hammers
- Closed Die Forging Capacity: Components ranging from 20 kg to 350 kg, using Zygmunt Hutta and Russian presses
- In-house tool & die manufacturing, CNC machining, heat treatment, and inspection facilities
Strict quality control and ISO 9001:2015 certified processes
Which Forging Process Is Right for Your Project?
Choose Open Die Forging if:
- You need a custom, large, or heavy component
- Your product will undergo extensive machining later
- You prioritize grain flow and mechanical strength
Choose Closed Die Forging if:
- Your component requires high accuracy and finish
- You’re manufacturing in bulk The part is intricate with defined geometries