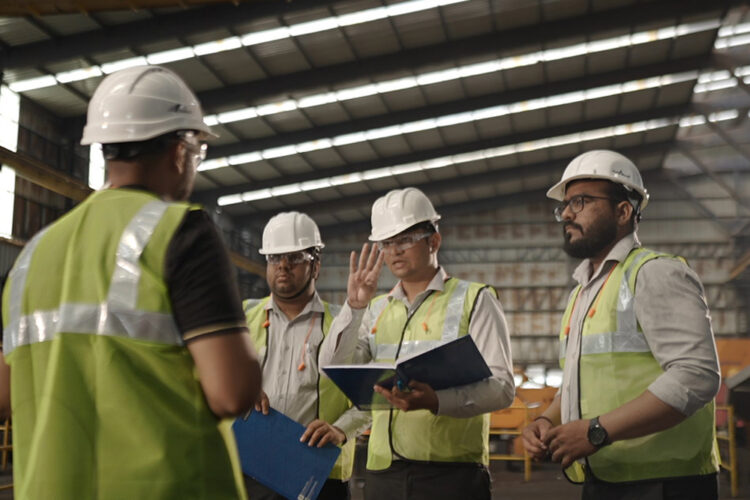
Forging Excellence: The Indispensable Role of HSE-Q-D-P at Shailesh Forging Works
In the robust world of metal forging, where raw strength meets precision engineering, success isn’t just about shaping metal; it’s about meticulously shaping a process that prioritizes every aspect from start to finish. At Shailesh Forging Works, a legacy of quality spanning over five decades, we understand that true forging excellence is built upon a robust foundation of HSE-Q-D-P: Health, Safety, Environment, Quality, Delivery, and Pricing. These aren’t just acronyms; they are the bedrock of our operations, ensuring superior products and sustainable practices. Let’s delve into why each of these pillars is crucial for a leading forging manufacturer.
1. Health, Safety & Environment (HSE): Our Non-Negotiable Commitment
The forging industry inherently involves high temperatures, heavy machinery, and powerful forces. Therefore, maintaining a paramount focus on Health, Safety, and Environment is not just a regulatory requirement but a moral imperative.
- Health & Safety: Our top priority is safeguarding our workforce. This involves:
- Rigorous Training: Comprehensive training programs on machine operation, heat stress management, and emergency procedures.
- Advanced PPE: Mandating and providing state-of-the-art Personal Protective Equipment (PPE) such as heat-resistant gloves, face shields, ear protection, and steel-toed boots.
- Machine Guarding: Implementing and regularly inspecting guarding devices and emergency stop controls on all forging presses, hammers, and other machinery to prevent mechanical hazards.
- Ergonomic Practices: Training in proper lifting techniques and promoting ergonomic solutions to prevent musculoskeletal injuries.
- Environment: We are committed to minimizing our ecological footprint. This includes:
- Ventilation & Air Quality: Utilizing advanced ventilation systems to manage fumes and dust, ensuring clean air in the forging area.
- Waste Management: Implementing robust waste management and recycling programs to reduce scrap and dispose of chemicals responsibly.
- Energy Efficiency: Continuously seeking ways to optimize energy consumption in our furnaces and operations.
A strong HSE culture fosters a secure and productive environment, ensuring that every team member returns home safely and contributes to a healthier planet.
2. Quality (Q): The Hallmark of Forging Durability
Quality is not an afterthought; it’s engineered into every forged component we produce. For critical applications in oil and gas, agro, and chemical industries, there’s no compromise on the integrity and performance of forged parts.
- Defining Forging Quality: Forgings must meet stringent industry standards, exhibiting exceptional mechanical properties, precise dimensional accuracy, and unwavering reliability. This means components are free from defects like cracks, porosity, or inconsistent grain flow.
- Achieving Superior Quality:
- Material Selection & Testing: Beginning with high-quality, uniform raw materials, rigorously tested for chemical composition and structural integrity.
- Precision Manufacturing: Leveraging advanced technologies, including open die, closed die, and seamless rolled ring forging, alongside state-of-the-art CNC and VTL machines for machining, ensuring precise shaping and dimensional accuracy.
- Process Control: Meticulous monitoring and adjustment of temperature, pressure, and force throughout the forging and heat treatment processes (normalizing, tempering, annealing).
- Rigorous Quality Assurance: Implementing multi-stage inspection and non-destructive testing (NDT) to identify any anomalies, coupled with continuous improvement protocols to prevent defects and minimize rework and scrap.
- ISO 9001-2015 Certification: Our certification reflects our adherence to global quality management standards, ensuring consistent excellence.
High-quality forgings lead to reduced warranty claims, increased customer satisfaction, and a stronger reputation in the market.
3. Delivery (D): On-Time, Every Time
In today’s fast-paced industrial landscape, on-time delivery is as critical as product quality. Delays can halt production lines, lead to costly penalties, and damage customer relationships.
- Customer Satisfaction & Loyalty: Meeting promised delivery dates builds trust and fosters long-term partnerships.
- Competitive Advantage: Consistent on-time delivery sets a manufacturer apart in a competitive market, attracting and retaining clientele.
- Operational Efficiency: Achieving high OTD rates signifies well-optimized production planning, efficient resource allocation, and a streamlined supply chain.
- How We Ensure Timely Delivery:
- Robust Production Planning: Efficient scheduling and real-time production monitoring identify and address bottlenecks proactively.
- Inventory Management: Maintaining an extensive in-house raw material inventory (over 30 grades) minimizes delays caused by material shortages.
- Predictive Maintenance: Regular maintenance and checks on our machinery reduce unexpected downtime.
- Global Logistics Partners: Collaborating with reliable logistics providers ensures efficient and timely dispatch from our extensive warehousing facilities.
Our commitment to prompt delivery reflects our dedication to your operational success.
4. Pricing (P): Value-Driven and Transparent
While quality and reliability are paramount, competitive and transparent pricing is essential for long-term partnerships. Understanding the factors that influence the cost of forged parts helps in making informed decisions.
- Factors Influencing Forging Costs:
- Material Selection: The type and grade of alloy significantly impact the overall cost.
- Tooling & Setup: Custom dies and setups for specific part geometries contribute to initial costs, especially for smaller volumes.
- Production Volume: Economies of scale typically result in lower unit costs for larger production runs.
- Complexity & Customization: Highly intricate designs or specialized requirements can increase manufacturing complexity and cost.
- Labor & Overhead: Efficient operations and automation help manage these costs effectively.
- Quality Control & Testing: Investment in rigorous quality assurance programs ensures defect-free products, reducing hidden costs associated with rework or field failures.
- Transportation & Logistics: Efficient dispatch and global partnerships help optimize delivery costs.
At Shailesh Forging Works, we strive to offer value-driven pricing, balancing advanced manufacturing capabilities, unwavering quality, and reliable delivery to provide the most cost-effective solutions for your forging needs.
The Interconnected Pillars of Forging Success
HSE, Quality, Delivery, and Pricing are not isolated elements; they are deeply interconnected. A strong HSE culture prevents accidents that could disrupt production and impact delivery. Uncompromising quality reduces scrap and rework, leading to more efficient production and ultimately, better pricing. Reliable delivery is a direct outcome of efficient processes, underpinned by both safety and quality. Fair pricing ensures the long-term viability necessary to invest in all these critical areas. At Shailesh Forging Works, this holistic approach defines our operations. It’s how we continue to forge not just metal, but enduring partnerships built on trust, excellence, and shared success. Ready to partner with a forging leader committed to your success?