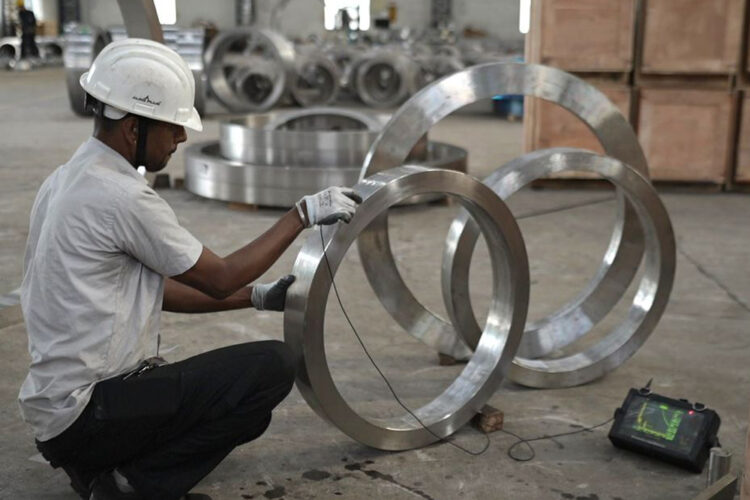
Forging Perfection: Why Rigorous Quality Checks are Non-Negotiable for Seamless Rolled Rings
In the demanding world of industrial machinery and critical infrastructure, components are not just parts; they are the lifelines of entire systems. This is especially true for seamless rolled rings, integral elements found in everything from jet engines and wind turbines to heavy-duty bearings and oil & gas flanges. At Shailesh Forging Works, we understand that for these critical components, there’s no room for error. That’s why our dedication to Ring Rolling & Quality Checking goes beyond mere compliance – it’s a fundamental commitment to safety, performance, and unwavering reliability.
The Power of Seamless Rolled Rings: Strength in Simplicity
Seamless rolled rings are circular metal components created through a highly specialized forging process. Unlike rings made by welding or casting, these are formed from a single piece of heated metal, which is then expanded and shaped between rolls. This process imparts a continuous, optimized grain flow that follows the contour of the ring. Why are they so critical? This unique grain structure bestows exceptional mechanical properties: superior strength, enhanced toughness, and outstanding resistance to fatigue and stress fractures. This makes them indispensable in applications where:
- High Stresses & Temperatures are Common: e.g., jet engine components, turbine parts in power generation.
- Reliability is Paramount: e.g., large bearings, heavy machinery gears.
- Leak Prevention is Crucial: e.g., flanges and valves in oil & gas pipelines.
- Safety is Non-Negotiable: Any failure could lead to catastrophic consequences, including equipment damage, environmental hazards, and, most importantly, loss of life.
Why Quality Checks are Not Just Necessary, But Imperative
Given the high-stakes environments in which seamless rolled rings operate, any defect-no matter how minor-can lead to disastrous outcomes. A tiny inclusion, an internal crack, or a dimensional inaccuracy can compromise the entire system, resulting in:
- Catastrophic Failures: Leading to explosions, collapses, or other severe accidents.
- Downtime & Production Losses: Equipment failure translates directly to lost revenue and operational inefficiencies.
- Expensive Repairs & Replacements: The cost of fixing or replacing critical components far outweighs the investment in rigorous quality control.
- Reputational Damage: A single component failure can severely erode trust and market standing.
- Regulatory & Legal Ramifications: Non-compliance with safety standards can lead to severe penalties.
This is precisely why every seamless rolled ring at Shailesh Forging Works undergoes a comprehensive suite of quality checks, ensuring that each piece not only meets but exceeds industry benchmarks and customer specifications.
The Arsenal of Assurance: All Types of Testing
Our commitment to quality translates into a multi-faceted testing approach, encompassing both non-destructive and destructive methods to guarantee the integrity of every ring.
Non-Destructive Testing (NDT): Inspecting Without Impairing
NDT methods allow us to meticulously examine the internal and surface integrity of the forged rings without causing any damage, ensuring they are fit for purpose.
- Ultrasonic Testing (UT): Using high-frequency sound waves, UT detects internal flaws, voids, or material inconsistencies that might not be visible on the surface. It’s crucial for identifying potential weak spots deep within the material.
- Magnetic Particle Testing (MT): For ferromagnetic materials, MT applies a magnetic field to the ring. Surface and near-surface cracks or discontinuities cause magnetic flux leakage, attracting fine magnetic particles (applied as a powder or suspension), making the flaws visible.
- Dye Penetrant Testing (PT): This method is used to detect surface-breaking defects in non-porous materials. A liquid penetrant is applied, allowed to dwell, and then removed, with a developer drawing out any penetrant trapped in surface flaws, making them visible.
- Positive Material Identification (PMI): Utilizing technologies like X-ray fluorescence (XRF), PMI verifies the chemical composition of the alloy, ensuring the correct material grade has been used as per specifications.
- Visual Inspection: Trained eyes perform initial checks for surface irregularities, proper finish, and any obvious signs of defects.
- Dimensional Inspection: Using precision instruments, we meticulously check outer diameter (OD), inner diameter (ID), height, and other critical dimensions to ensure they adhere to strict tolerances, often employing advanced CMMs (Coordinate Measuring Machines).
Destructive Testing (DT): Proving Material Integrity
While NDT checks for defects, destructive testing confirms the material’s mechanical properties, ensuring it can withstand the forces and conditions it will encounter in application. Test samples are taken from the forged rings and subjected to rigorous evaluation.
- Tensile Testing: This test measures a material’s strength, including its yield strength (the point at which it begins to deform permanently) and ultimate tensile strength (the maximum stress it can withstand before breaking). It also assesses ductility (elongation and reduction of area).
- Impact Testing (Charpy V-Notch): This test determines a material’s ability to absorb energy before fracturing, especially at low temperatures, crucial for components in cold environments.
- Hardness Testing (Brinell, Rockwell, Vickers): These tests measure the material’s resistance to permanent indentation, indicating its strength and wear resistance.
- Micro-cleanliness & Microstructure Analysis: Metallurgical analysis examines the material’s internal grain structure, cleanliness (absence of inclusions), and heat treatment effectiveness, crucial for understanding its long-term performance and fatigue life.
- Chemical Analysis: While PMI provides rapid verification, a more detailed chemical analysis confirms the precise elemental composition, ensuring it meets the specified alloy requirements.
Shailesh Forging Works: Forging with Unwavering Assurance
At Shailesh Forging Works, every seamless rolled ring is a testament to our commitment to precision and safety. Our comprehensive quality control protocols, adhering to stringent international standards like ISO 9001-2015 and often customer-specific certifications (e.g., API, ASTM, EN), ensure that each component leaving our facility is robust, reliable, and ready to perform under the most demanding conditions. From the meticulous control of our ring rolling process to our state-of-the-art testing laboratories, we leave no stone unturned. Because when it comes to critical applications, quality isn’t just an advantage; it’s an absolute necessity. Partner with Shailesh Forging Works for seamless rolled rings, where quality is always assured.