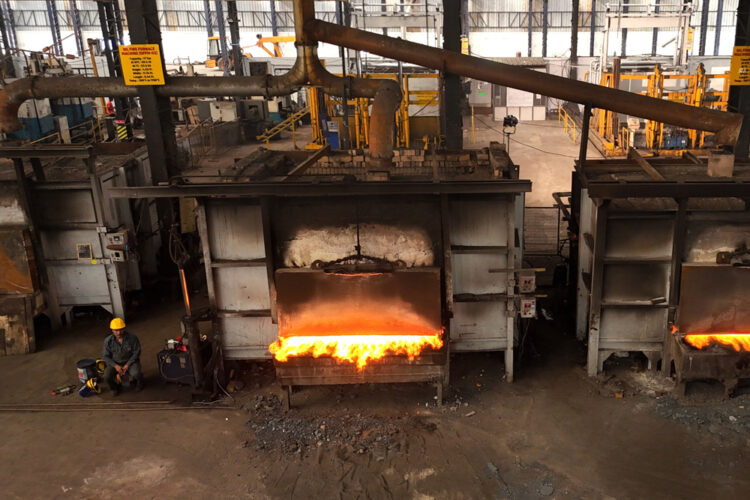
The Perfect Heat: Why Ideal Forging Temperature is Critical for Quality at Shailesh Forging Works
In the art and science of metal forging, temperature is not merely a number on a dial; it’s the invisible hand guiding the transformation of raw material into a component of exceptional strength and integrity. At Shailesh Forging Works, with our decades of expertise, we understand that achieving good quality forging hinges on hitting – and maintaining – the ideal temperature for each specific material. This precision is why some materials demand 950-1000°C, while others require 1200-1250°C, or even beyond.
The Science Behind the Heat: Why Temperature Matters So Much
Forging is a hot working process, meaning the metal is plastically deformed above its recrystallization temperature. At this elevated temperature, the material becomes significantly more ductile and malleable, allowing it to be shaped under compressive forces without fracturing. Here’s why precise temperature control is paramount:
- Plastic Deformation: Heating the metal to its ideal forging temperature softens it, reducing its flow stress. This allows for easier deformation, requiring less force and reducing wear on expensive dies and tooling.
- Grain Structure Refinement: Forging above the recrystallization temperature allows new, finer, and more uniform grain structures to form as the metal is deformed. This process eliminates internal stresses, closes pores, and breaks up harmful inclusions, significantly enhancing the material’s strength, toughness, and fatigue resistance.
- Achieving Desired Properties: The final mechanical properties of a forged component are highly dependent on the grain structure achieved during forging and subsequent cooling. Correct temperature ensures optimal microstructural development.
It’s Not One Size Fits All: Different Steels, Different Heats
The “ideal” forging temperature is not universal; it’s highly specific to the material’s chemical composition and metallurgical characteristics. What’s perfect for one alloy could be catastrophic for another.
- Carbon Steels (e.g., Mild Steel, Medium Carbon Steel): These often have broader hot working ranges. For instance, low to medium carbon steels are typically forged between 1100°C and 1200°C, while high carbon steels might be worked at slightly lower initial temperatures, ranging from 1000°C to 1200°C. The goal is to ensure the material is above its recrystallization temperature for effective deformation and grain refinement.
- Alloy Steels: With additional alloying elements like chromium, nickel, and molybdenum, alloy steels often have different forging windows. Depending on the specific alloy, their forging temperatures can range from 850°C to 1150°C or sometimes higher, requiring careful monitoring to avoid issues like hot shortness.
- Stainless Steels (Austenitic, Martensitic, Duplex): These materials, known for their corrosion resistance, also have specific temperature requirements. Many stainless steel grades are forged between 927°C and 1260°C (1700°F and 2300°F). For example, popular grades like 304 and 316 Stainless Steel fall within this higher end, while duplex stainless steels like 2205 have a narrower range (1020°C and 1100°C) requiring even more precise control.
The Perils of Incorrect Temperature: What Can Go Wrong
Deviating from the ideal forging temperature window, whether too cold or too hot, can severely compromise the quality and integrity of the forged product:
- Forging Too Cold (Below the Ideal Range):
- Cracking and Tearing: The metal is not ductile enough, leading to internal or external cracks as it resists deformation.
- Incomplete Die Fill: The material may not fully flow into the die cavities, resulting in incomplete or improperly shaped parts.
- Increased Stress & Die Wear: Higher forces are required, leading to accelerated wear and potential damage to forging dies and equipment.
- Strain Hardening: The material hardens prematurely, negating the benefits of hot working.
- Forging Too Hot (Above the Ideal Range):
- Grain Growth: Excessive heat can lead to undesirable grain growth, reducing the material’s toughness and fatigue life.
- “Burning” or Overheating: The material can suffer incipient melting or oxidation at grain boundaries, leading to irreversible damage, making the part brittle and unusable.
- Decarburization: Loss of carbon from the surface, affecting surface hardness and wear resistance.
- Reduced Mechanical Properties: The very properties that forging aims to enhance can be degraded, making the part unsuitable for its intended critical application.
Precision Heating at Shailesh Forging Works
Achieving and maintaining the ideal forging temperature is a hallmark of our quality commitment. At Shailesh Forging Works, we employ:
- Advanced Furnaces: Our oil and electric heating furnaces are designed for precise temperature control and uniform heating of billets and ingots.
- Continuous Monitoring: We utilize sophisticated non-contact temperature measurement systems, such as infrared pyrometers and thermocouples, to continuously monitor the temperature of the metal throughout the preheating, soaking, and forging stages.
- Metallurgical Expertise: Our experienced metallurgists and engineers determine the exact temperature profiles and soaking times required for each specific material and part geometry, ensuring optimal grain structure and mechanical properties.
- Controlled Environment: We manage the cooling rate of components post-forging to further refine the microstructure and achieve desired hardness and strength.
By meticulously controlling every degree of the forging process, Shailesh Forging Works ensures that each component we produce possesses the superior quality, durability, and performance required for the most demanding industries. It’s not just about heating metal; it’s about engineering excellence from the inside out. Looking for forged components where temperature precision translates to unparalleled quality?