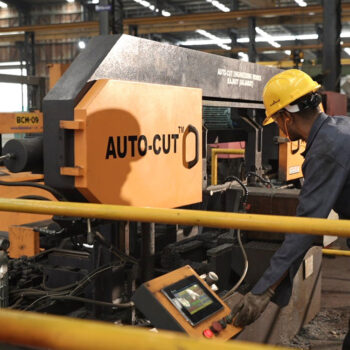
Cutting Facility
Our cutting unit features 34 advanced CNC-controlled band saw machines, enabling precision metal cutting from 50 mm to 650 mm. This facility is designed for high-speed, automated processing and ensures micron-level accuracy, consistent quality, and increased throughput for heavy-duty forging applications.
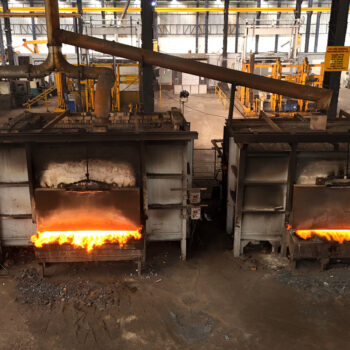
Heating Facility
Our heating division has API 6A and ASTM A991 calibrated oil-fired furnaces, ensuring precise, reliable, and compliant heat treatment for forged components. With a combined capacity of 15,000 kgs, our thermal processing facility guarantees consistent heating performance for demanding industrial applications.
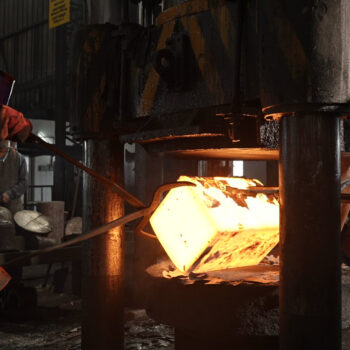
Open Die Forging
We specialize in open die forging for large metal components, using hydraulic presses up to 2500 MT and a 5 MT drop belt hammer. Our up setting forging process ensures superior grain structure, unmatched strength, and precision shaping for custom industrial applications.
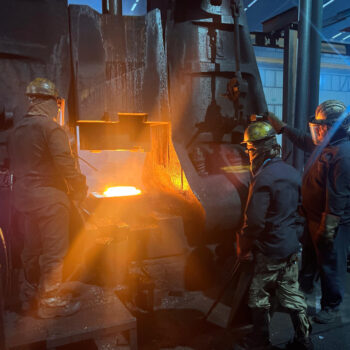
Closed Die Forging
Our closed die forging capabilities deliver high-strength, net-shaped metal components with tight tolerances. Equipped with Zygmunt Hutta and Russian Arrie hammers up to 8 tons, we offer reliable forging solutions for complex and detailed metal parts across industries.
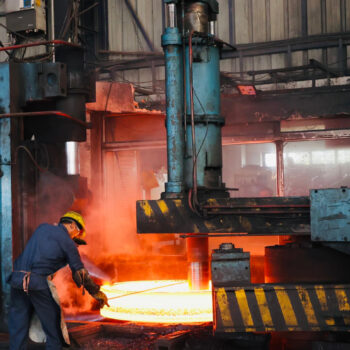
Seamless Rolled Ring Manufacturing
We produce seamless rolled rings with diameters from 300mm to 3000mm and heights up to 600mm, which is ideal for heavy-duty industrial applications. Custom profiles are available upon request.
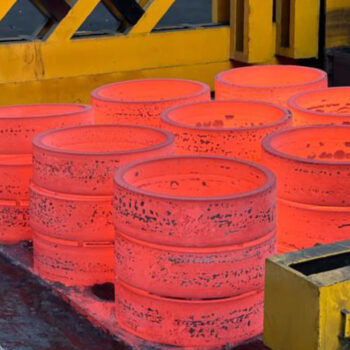
Heat Treatment Facility
Our advanced heat treatment facility features two fully automated gas-fired water quench furnaces, capable of handling 10 MT per batch. We specialize in Normalizing, Tempering, and Annealing using box-type furnaces (3.2m x 3.2m x 1.2m), ensuring optimal mechanical properties and superior product quality for critical applications.
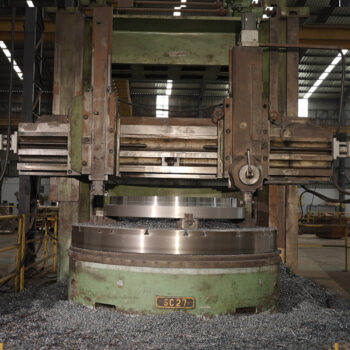
CNC & VTL Machining Facility
Our machining facility is equipped with 15 VTL machines, 4 CNC VTL machines, 4 CNC machines, and 2 radial drilling machines, capable of processing seamless rings up to 3000 mm in diameter. With high-precision equipment and expert machinists, we deliver components that meet exacting drawing tolerances and surface finish standards.
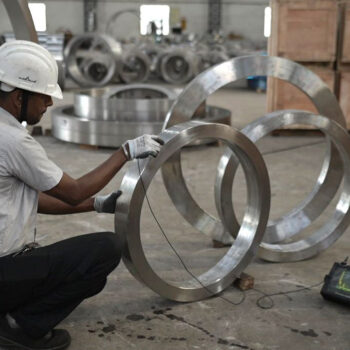
Advanced Inspection Facility
Our inspection facility features cutting-edge ultrasonic testing, hardness testing, dimensional inspection, and magnetic particle inspection to ensure every product meets stringent quality standards. We guarantee precision, reliability, and defect-free components through comprehensive quality assurance protocols.
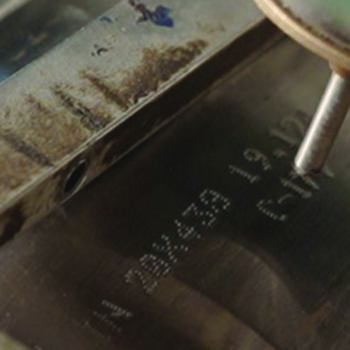
Marking Facility
We provide permanent product identification using die stamping, dot marking, and engraving techniques. Our marking facility ensures full traceability, compliance with international standards, and supports easy tracking across the supply chain.
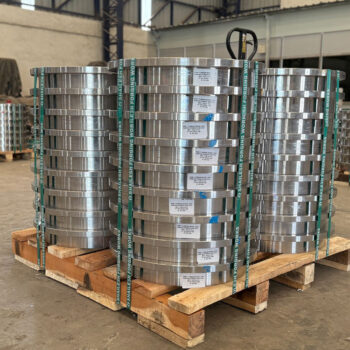
Packing & Dispatch Facility
Our dedicated packing and dispatch unit ensures that each component is securely packed using wooden crates, shrink wraps, or as per customer specifications. We prioritize damage-free transport, clear labeling, and timely dispatch to both domestic and international clients.