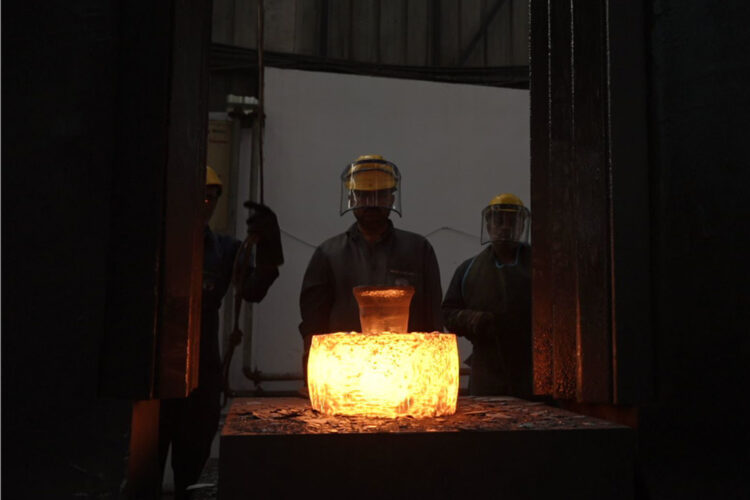
Forging is one of the oldest and most trusted metalworking techniques in the manufacturing world. From aerospace and oil & gas to railways and renewable energy, forged components power the backbone of heavy industry. Yet, despite its widespread use and proven strength, forging still faces misconceptions-especially in the era of rapid prototyping, casting, and 3D printing. At Shailesh Forging Works, we’ve been perfecting the science of open die, closed die, and ring forging since 1980. And today, we’re here to bust the Top 5 Myths About Forging and help you make an informed decision for your project.
Myth 1: Forging Is Outdated – Casting or Machining Is More Modern
Reality: Forging is not only relevant but essential in modern engineering. In fact, many high-performance industries like aerospace, defense, and power generation rely exclusively on forged parts due to their superior strength and grain flow. Why forging still leads:
- Eliminates internal voids & porosity
- Improves mechanical integrity
- Ideal for critical load-bearing parts
Myth 2: Forging Only Works for Simple Parts
Reality: Modern forging-especially closed die forging and CNC-controlled ring rolling-can produce complex geometries with tight tolerances. From gear blanks and valve bodies to pellet dies and slip segments, forged parts can be both intricate and dimensionally precise. At Shailesh Forging Works, we offer:
- Custom tooling and dies
- Complex forgings from 20 kg to 4 MT
Integration with CNC machining & inspection
Myth 3: Forged Components Need Too Much Post-Machining
Reality: Not anymore. Advances in closed die forging and near-net-shape forging drastically reduce the amount of post-processing required. In many cases, forged parts can be delivered semi-machined or fully machined, depending on client needs. Plus, we offer in-house:
- CNC machining (VTL, radial, lathe)
- Surface finishing and tolerance correction
- Dimensional inspection and hardness testing
Myth 4: Forging Is Too Expensive for Small Batches
Reality: While large volumes benefit from economies of scale, open die forging and custom ring forging are extremely cost-effective for low to medium production runs-especially for large components or non-standard profiles. Forging benefits for small runs:
- Lower tooling cost (especially open die)
- Faster turnaround than casting
- Higher strength = less replacement & maintenance
Myth 5: All Forging Methods Deliver the Same Results
Reality: Each forging technique has its purpose. The choice between open die, closed die, and ring rolling depends on the part’s:
- Size
- Material
- Shape complexity
- Volume requirement
Quick Guide:
Forging Type | Best For |
Open Die | Large custom shapes (shafts, discs) |
Closed Die | High-volume, precision parts |
Ring Rolling | Seamless rings (gear, bearing, flange) |
At Shailesh Forging Works, we offer all three, plus integrated heat treatment and inspection, to meet your exact specifications.
Why Forging Still Reigns in Engineering
- Superior grain flow
- Stronger fatigue resistance
- Better dimensional stability
- High-pressure performance
- Longer life under thermal and mechanical stress
From standard flanges to custom alloy forgings, nothing beats a forged part when performance matters most.